CAPITOLO IV Caso di studio: modellizzazione di una Manufacturing Supply Chain
4.11 Comportamento del modello di produzione
Per iniziare a testare il modello la tabella 4.8 mostra i parametri che saranno considerati come costanti
per un'azienda manifatturiera.
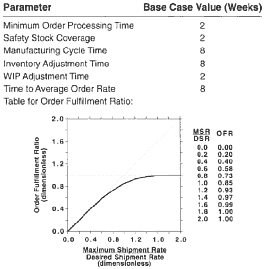
Figura 4.8- Parametri di base per il modello produttivo
Mentre "Minimum order processing time" è 2 settimane, l'azienda desidera uno stock di sicurezza (safety stock) di 2 settimane
addizionali di copertura. Dati i valori per order fulfillment function, inventory coverage, uguale al minimum order processing
time risulterebbe, in un livello di servizio dell'85%.
Aggiungendo uno stock di sicurezza uguale a 2 settimane addizionali di domanda attesa (expected demand) significa che il tasso
massimo di spedizione (maximum shipment rate) sarebbe 2 volte il tasso desiderato quando inventory eguaglia il suo livello
desiderato, abilitando l'azienda a riempire il 100% degli ordini.
Questo primo semplice modello che riguarda la gestione del magazzino senza considerare ancora la gestione e il reperimento
dei materiali e gli ordini arretrati è stato implementato con Powersim e il diagramma strutturale è riportato in figura 4.9.
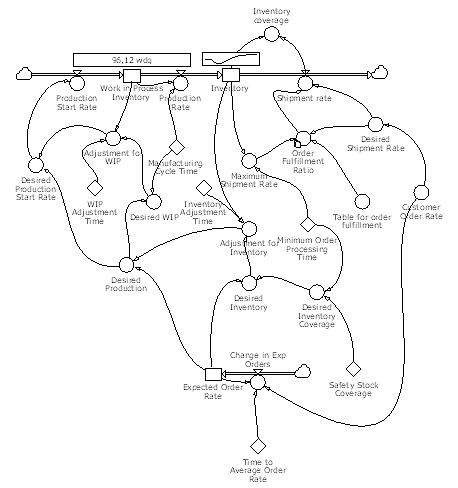
Figura 4.9- Struttura della gestione del magazzino
Come visto per l'esempio del capitolo precedente, tramite il software di simulazione scelto è possibile visualizzare tramite
grafici di tempo l'andamento delle variabili, che costituiscono la struttura del sistema, e quindi poterne studiare
il comportamento.
La figura 4.10 mostra la risposta dell'azienda ad un inaspettato incremento del 20% negli ordini dei clienti.
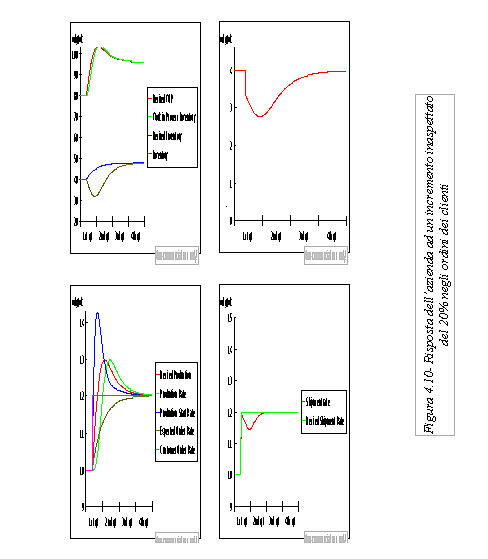
L'iniziale customer order rate è di 10 "widgets/week" . Desired shipment rate aumenta immediatamente dopo l'improvviso incremento
in domanda. Inventory coverage immediatamente cade dal suo iniziale valore di 4 weeks a 3.33 weeks.
Nell'istante in cui customer order rate aumenta, inventory non è ancora cambiato, così Maximum Shipment Rate rimane lo
stesso (20 widgets/week). L'incremento degli ordini del 20% riduce il rapporto tra maximum e desired shipment da 2 a 1.67.
Order fulfillment ratio a questo punto è sopra il 99%, cosi l'azienda è inizialmente capace di coprire quasi tutti gli
ordini entranti, nonostante l'incremento.
Tuttavia, poiché la produzione continua all'iniziale tasso di 10 "widgets/week", inventory cade sotto il livello iniziale.
Come inventory cade, così l'azienda non è più in grado di spedire la merce. Dopo circa 7 settimane dall'improvvisa variazione
di domanda, order fulfillment ratio scende al 95% causando la perdita di affari dell'azienda (e la sua reputazione come
fornitore affidabile).
Il divario tra il magazzino desiderato e quello attuale costringe desired production ad alzarsi al di sopra di expected orders.
Questo fa si che si apra un divario tra il livello attuale e quello desiderato di WIP. Di conseguenza, poiché WIP è incrementato
da production start rate, questo cresce ulteriormente al di sopra di desired production rate.
Col passare del tempo l'azienda riconosce che l'iniziale incremento in domanda non è una casuale battuta d'arresto e la
sua previsione di domanda gradualmente cresce.
Date le 8 settimane di livellamento per la previsione, serve circa mezzo anno per correggere il 95% della gestione per il
nuovo tasso di ordine.
In questo periodo, il sistema non può realizzare un equilibrio bilanciato: se inventory e WIP inventory fossero stati uguali
al loro valore desiderato, la produzione uguaglierebbe la previsione della domanda, che, dal momento che è minore degli
ordini causa la caduta del magazzino.
Come expected orders cresce, così fa anche desired inventory, aggiungendo un divario tra il magazzino attuale e quello
desiderato e incrementando desired production ulteriormente.
Production starts raggiunge il massimo aumentando del 42% circa rispetto al livello iniziale dopo circa 4 settimane dopo
l'improvviso aumento di domanda.
Il rapido incremento in Production starts subito riempie la fornitura di WIP ma la produzione è indietro di 8 settimane.
La produzione non sorpassa shipment se non dopo che sono passate 6 settimane; attraverso questo periodo di tempo inventory
continua a scendere nello stesso modo in cui desired inventory cresce.
Inventory cessa di scendere quando la produzione uguaglia le spedizioni.
Tuttavia il sistema non è ancora in equilibrio a causa del grande divario tra l'inventario desiderato e quello attuale
e tra orders e expected orders.
Production eventualmente cresce al di sopra di shipments, provocando la crescita del magazzino, prima che esso raggiunga
eventualmente il nuovo, e più alto, livello desiderato.
E' da notare che il massimo della produzione si raggiunge dopo circa ¼ di anno dopo la variazione degli ordini, molto
più delle 8 settimane scelte come ritardo di produzione.
La simulazione del sistema rivela alcuni aspetti fondamentali del comportamento di una supplì chain:
- Primo, l'iniziale risposta dell'azienda ad un inaspettato incremento nella domanda è un calo del magazzino. Il ritardo nella produzione (production delay) comporta un inevitabile calo iniziale del livello di magazzino ed è una fondamentale conseguenza della struttura fisica del sistema. La riduzione del magazzino contrasta bruscamente con il desiderio dell'azienda di tenere più scorte quando la domanda aumenta;
- Secondo, l'amplificazione dell'incremento improvviso della domanda è inevitabile. Poiché il livello magazzino deve inizialmente cadere, l'unico modo per incrementarlo al suo iniziale livello e quindi elevarlo al nuovo, più alto livello desiderato è quello di far eccedere la produzione rispetto alle spedizioni. Production deve passare parecchio al di sopra di shipment rate per creare un magazzino che eguagli il nuovo livello desiderato. Production starts deve elevarsi ancora di più cosicché il livello di WIP può portarsi ad un livello consistente con un più alto tasso di produttività.
- Terzo, la correzione alla produzione raggiunge il suo massimo più o meno quando inventory raggiunge il suo minimo. Inventory tocca il minimo solo dopo che la produzione è finalmente cresciuta abbastanza da eguagliare le spedizioni (shipments). Questa fase di ritardo caratteristica della maggior parte delle supplì chains, è una fondamentale ed inevitabile conseguenza della struttura fisica di scorte e flussi.